Advances in plastics and bioplastics
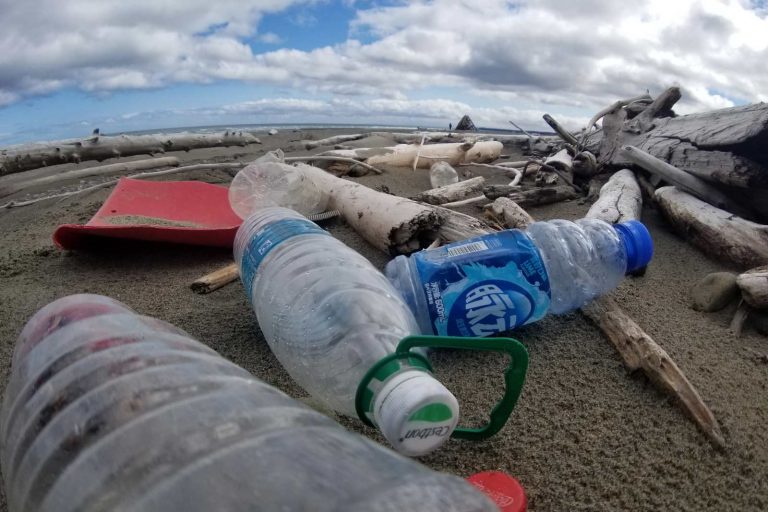
Toward a Plant-based Future
Most of the objects and gadgets we use on a daily basis contain oil- and natural-gas-liquid-based polymers that at present have no non-plastic substitutes. These include cellphones, computers, packaging, tools for medical use, toys and even composite materials used to build cars, trains, planes and spacecraft. But researchers are cooking up bioplastics — monomers and polymers derived from renewable resources. Many of these initiatives are in the early stages and have not been deployed on a global scale. And some research has shown that bioplastics are not a silver bullet in the fight against plastic pollution because even when they are biodegradable and compostable, they don’t tend to break down unless they are zapped with large amounts of heat or sunlight. While these latest advances in plastic production don’t solve the issue of overconsumption of goods in the Western world, they do offer a way to think outside the petrochemical box. Here are some examples.
Bio-PET
Replacing PET, or polyethylene terephthalate, bio-PET is derived from by-products from the agricultural industry. This plant-based resin comes from sources such as hay and sugarcane, and, like petroleum-based PET, is recyclable and used to make water and pop bottles.
Avocados
Mexican company Biofase turns discarded avocado pits into a bioplastic used to make cutlery and drinking straws. Biofase takes some 130 tonnes of avocado pits each month from guacamole and avocado-oil manufacturers, keeping the seeds away from landfills. With this raw material, the company creates one plastic that biodegrades in 240 days and another that degrades in a compost heap.
Mushrooms
Mushrooms grow from a root structure called mycelium. This same foundation is converted by the company Ecovative Design into the structural component of two types of bioplastics: MycoComposite and MycoFlex. Mycocomposit, when mixed with organic agricultural by-products, can be used to make rigid plastics, while MycoFlex is a foam-like plastic used in protective packaging that’s already being used by such companies as IKEA and Dell.
Corn
Polylactic acid, or PLA, is derived from corn with the help of bacteria that produce lactic acid, which can be used to create a polymer resin. The potential applications are numerous, including clothing, bottles, mobile phone casings, credit cards and food packaging. PLA can also be made from organic waste and transformed into multilayer food packaging that can be composted along with any leftovers inside.
Seaweed and Algae
Agari — made from agar, a powder derived from red algae — is an experimental polymer developed by Icelandic product designer Ari Jónsson. Used for bottles, it holds up as long as it’s in contact with water, but as soon as you drink the content of the bottle, it starts to biodegrade. You can also compost it. In Indonesia, the start-up Evoware makes compostable — and edible — seaweed sachets for food items such as instant coffee and noodle seasoning, with more applications on the drawing board. And in the Netherlands, designers Erik Klarenbeek and Maartje Dros grow algae that they dry and process into a substrate used to print 3D objects.
Lobster and Crab Shells
Scientists at Montreal’s McGill University have come up with a way to transform lobster and crab shells into a biodegradable plastic derived from chitin. Chitin comes from the exoskeletons of some shellfish and insects, and researchers at the University of Georgia have used its derivate chitosan to create flexible food packaging, while Harvard University scientist turned to chitosan to make disposable medical products, including sutures and bandages.
Trees
Pinene is a chemical compound extracted from pine-tree needles. Researchers from the Centre for Sustainable Chemical Technologies at the University of Bath, in the U.K., have developed a way to include this pulp-and-paper-industry leftover as a replacement for crude-oil-based caprolactone, which today is used to make some degradable polymers more flexible. (The same team is also looking into limonene, another terpene, found in citrus fruit, as a substitute for plastic.) And in Finland, a team of researchers at the VTT Technical Research Centre, is developing compostable plastics from wood cellulose. These polymers can be made into layered plastics that protect food and other perishables from moisture and oxygen.
Sugarcane
Polyethylene, the most common plastic, is made by polymerizing ethylene synthesized from petroleum-derived ethanol. But ethylene can be made from ethanol that’s derived from sugarcane, as the Brazilian company Braskem is doing, and then used to replace petrochemicals for the manufacture of I’m Green Polyethylene plastic.
Food and agricultural waste
As for textiles, there are currently several initiatives using food and agricultural waste to replace synthetic fabrics (and animal-derived materials such as leather), as well as buttons and fasteners for garments. This transformation keeps waste from being left to rot and release methane gas, or being burned , which creates carbon monoxide emissions. London-based Piñatex uses pineapple leaf fibres to make vegan leather, while Italian company OrangeFibre makes textiles for clothing from… yes, discarded orange peels. Circular Systems takes rice straw, banana waste, hemp- and flax-seed straw and pineapple leaves to create not only textiles but also packaging.